Ever wondered if a square keg would work? This clever patent shows that it can be done. No indication how much pressure it could safely handle. It would need to stay less than 5 ATM with a good pressure release valve and be safely tested first.
https://havencrest-microbrewery.blogspot.com/2016/08/rectangular-container-for-aging-of.html
https://havencrest-microbrewery.blogspot.com/2016/08/rectangular-container-for-aging-of.html
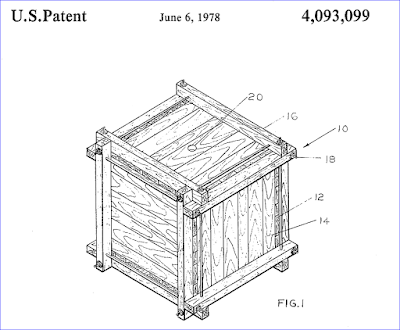